日前,陕西北元集团水泥有限公司技术员工自行对一、二线水泥入库胶带提升机进行技改,不仅实现了节能降耗,提升了设备运转率,而且大大提高了生产效率。经过技改后,每次检修可为公司节约成本约5万元。
即将进入夏季,水泥销售将迎来产销高峰,为保障产品有效供应,陕西北元集团水泥有限公司挖潜扩能,通过对一、二线水泥入库胶带提升机进行技改,不仅实现了节能降耗,提升了设备运转率,而且大大提高了生产效率。
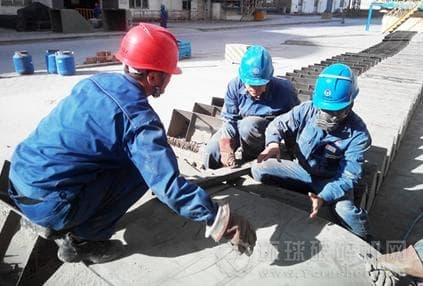
对胶带提升机进行技改
此次技改主要呈现出三大亮点:一是缩短了胶带长度;二是减少了料斗;三是提高了尾轮位置。虽然看似都是小改造,却实现了节能、降本、降耗,提升了设备运转率、提高经济效益。
设备技术员薛锦卫介绍到,从前的斗提相当于“小马拉大车”,电耗非常大,通过此次创新性改造,一、二线每条线的胶带缩短了约40米,料斗减少了100个,就胶带和料斗自身重量来讲,大大减轻了设备运转负荷,从而降低能耗。以前的提升机构造存在部分缺陷:一是成品水泥下落距离远,对胶带和料斗的冲击力比较大,经常出现料斗磨破的现象;二是由于出磨水泥的温度较高,会加速胶带的老化;三是紧固料斗的螺栓及料斗长期在高温环境下运转,容易软化、变形,导致脱落,尤其在水泥营销高峰期,这是一个重大的安全隐患。通过此次将斗提尾轮提升至成品斜槽处,彻底解决了这一问题,水泥直接落入斗提,一方面避免了落差大对斗提的冲损,另一方面也避免了高温对皮带的影响。通过此次创新有效降低了检维修和配件采购成本,胶带一米约800元,料斗每个约170元,经过技改后,每次检修可为公司节约成本约5万元。
故障频发率低,恢复周期短,生产效率大幅提升。以前由于结构不合理,提升机故障频发,几乎每个班都会出现提升机故障,而每次抢修恢复运转*快也需1小时,按照台时120吨每小时计算,一天就是360吨,如果按一年计算就会损失131400吨水泥,相当于一个月的产量。通过此次技改,缩短了水泥的下落距离,而且“即落即提”,斗提调停后,下方也不会像以前一样沉积过多物料,经电气仪表工检查后即可立刻启动设备,大大降低了抢修强度,缩短了故障恢复周期,生产效率大大提高。